Just two hours
from Mexico
Las operaciones de Sohnen tienen su sede en Santa Fe Springs, California, donde opera dos instalaciones a gran escala que emplea a más de 150 personas. Una de las dos instalaciones actúa como el Centro Nacional de Recepción de Sohnen [National Receiving Center-NRC], donde el fabricante y las fuentes de suministro de los minoristas envían sus devoluciones de productos. Posteriormente, los productos se preparan para su envío a las instalaciones de Sohnen en Tijuana, México, para su procesamiento.
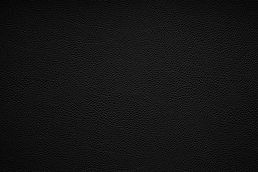
MANUFACTURERS

Managing dealer returns continues to be a significant challenge for all manufacturers. Maintaining the staff and facilities necessary to receive thousands of units in thousands of shipments requires significant resources and involve considerable costs that only increase every year. Even assuming that this may not be an issue for some Manufacturers, once the returns are received, the next step can be even more complicated; What to do with them? As their distribution grows, their volume of returns increases as well. If their distribution base also includes online merchants, then the problem is only amplified with the higher than normal return rates associated with those sales. For most Manufacturers, returns are at best, an afterthought and rarely given the attention or resources necessary. Sohnen has dedicated the past half century to developing a refined, focused and efficient process for dealing with product returns and also offers Manufacturers an entire suite of related services including:
1- Serving as a National Return Center
2- New Product Analysis
3- Production Data Reports
4- Financial Recovery
• Outright Purchase
• Fee For Service
• Revenue Sharing
• Fulfillment Services
5- True Recycling
6- New Inventory Product Modification Work
7- Controlled Distribution and End of Life Closeouts
Regardless of your specific needs, Sohnen can develop a custom approach that incorporates some or all of the above concepts. Although our primary focus over the years has been on consumer electronics and small appliances, we have also processed a wide variety of other product categories as well.
National Receiving Center
Sohnen contracts with a vast network of transportation providers to efficiently and reliably pick up Product Returns shipments from nationally based retailer return centers. Once received at Sohnen’s NRC, shipment accuracy by model and quantity is verified and subsequently shipped to Sohnen’s refurbishing plants in Tijuana, Mexico. The Returns Data captured by Sohnen at this point enables the manufacturer to issue the appropriate credit memos to their customers.


New Model Analysis
Sohnen produces a New Model Analysis report on the initial shipments received of all new model introductions. These reports are assembled by our Team of engineers to provide feedback on overall quality issues seen on the initial returns of a given product model. Test OK rates, Major Defects found, repair guidelines, parts required for repair work and overall conclusions as to the quality of the manufacturing and design of the products are provided back to the manufacturer.
Production Data Reports
All products processed by Sohnen are tracked by a proprietary bar code labeling system that follows each product from the point it starts the production process at Sohnen , all the way through to the final disposition to the final retailer or distributor. These reports are issued monthly and reference original serial numbers and retail source of the return. The reports allow Manufacturers to understand the design and manufacturing strengths and weaknesses of their products, as well as the return behavior of their retail partners.

True Recycling
If your company is truly committed to playing your part in supporting a healthy earth and “green” initiatives, you already know that the best form of recycling is “reuse”. Sohnen is the best way to accomplish this as 90% of everything we receive is returned back to the market as finished products. The 10% that cannot be refurbished is broken down by our own Team to their core materials such as plastic, copper, aluminum, steel, paper, Styrofoam and cardboard, all of which are the sent to companies who will reuse the materials to make new products. Sohnen’s plants boast full solar installations, rainwater recapture systems, on site water treatment plants and strategic use of skylights to illuminate production areas.


New Inventory Product Modification Work
From time to time, it is not unusual for any manufacturer to discover that the new condition inventory in their warehouse requires some type of mechanical or electronic modification to improve product performance or safety prior to being initially shipped to their retail outlets. Sohnen provides all of the resources necessary to quickly turn around large groups of inventory that require such work. With a standing support staff of over 1000 people, it is easy for Sohnen to realign our processes and people to respond to emergency situations that require large scale production requirements with short lead times.
Controlled Distribution of Refurbished Inventories or end of life closeouts
Over the past five decades, Sohnen has developed diverse markets to resell its refurbished products. Our customers are primarily based in the United States, but we also do a considerable amount of business in Mexico, South and Central America and the Caribbean. Regardless of location, most of our customers are long term accounts of Sohnen and comply with our requirements to accurately represent the products as refurbished and to avoid market conflict with the sales activities of our suppliers. This wide base of accounts are also prime outlets for closeouts of end-of-life new condition products as well as refurbished ones.
